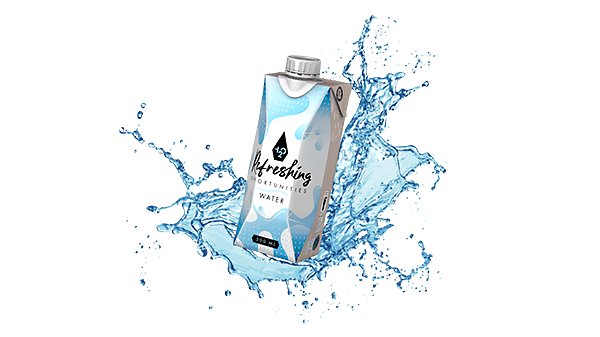
The global movement toward sustainable alternatives has thrust waterproof paper packaging into the spotlight. As brands and consumers ditch single-use plastics, the challenge lies in creating paper packaging that repels water without relying on toxic chemicals or non-recyclable materials. This blog explores how waterproof paper packaging bridges functionality and sustainability, including traditional laminates like aluminum foil and cutting-edge coatings.
1. What Does Waterproof Paper Packaging Mean?
Waterproof paper packaging refers to paper-based materials treated with barriers or laminations that prevent moisture penetration while maintaining recyclability or compostability. Solutions range from plant-based waxes to aluminum foil laminates. Key considerations include:
Safety: Avoiding PFAS, BPA, and other harmful substances.
Eco-Design: Compatibility with recycling/composting systems.
Performance: Balancing durability with environmental goals.
2. How to Make Waterproof Paper Packaging?
2.1 Traditional Methods
Paraffin Wax
- Process: Paraffin wax, a petroleum byproduct, is melted and applied via dipping, spraying, or extrusion.
- Applications: Ideal for frozen food boxes and bakery liners.
- Environmental Impact: Non-renewable and contributes to fossil fuel dependency. Soy or beeswax alternatives (renewable) are emerging but face challenges like ethical sourcing (beeswax) and agricultural land use (soy).
- Case Study: EcoCraft uses soy wax-coated paper for compostable sandwich wraps, reducing plastic use by 30%.
Polyethylene (PE) Lamination
- Process: A thin PE layer is heat-sealed to paper, common in milk cartons.
- Challenges: Recycling difficulties due to mixed materials; only 20% of U.S. facilities process PE-coated paper.
- Innovation: Tetra Pak integrates 20% sugarcane-based PE, cutting carbon footprint by 15%.
2.2 Eco-Friendly Alternatives
PLA (Polylactic Acid) Coatings
- Process: Derived from fermented cornstarch, PLA forms a compostable barrier.
- Limitations: Requires industrial composting (140°F for 90 days); ineffective in home composts.
Example: Chinet’s PLA-coated plates are commercially compostable but struggle in residential settings.
Water-Based Acrylics
- Chemistry: PFAS-free polymers suspended in water reduce VOC emissions by 50% vs. solvent-based coatings.
-
Performance: Effective for pizza boxes but less durable for liquids.
-
Regulatory Advantage: Compliant with EU’s PFAS bans, making them future-proof.
2.3 Advanced Innovations
Nanocellulose Barriers
- Technology: Plant-derived nanocrystals (3–5 nm thick) create ultra-thin, high-performance barriers.
- Applications: Metsä Group’s paper bottles for liquids showcase its potential.
- Cost: Currently ~$10/kg, but prices are dropping as production scales.
Seaweed Alginate
- Extraction: Sourced from brown seaweed, forming edible, marine-degradable films.
- Use Case: Notpla’s seaweed-coated condiment sachets degrade in weeks, winning the 2023 Earthshot Prize.
Silicone Coatings
- Durability: Heat-resistant up to 428°F, ideal for reusable baking sheets.
- Trade-off: Non-biodegradable but reduces waste via reusability.
2.4 Table Comparison of Waterproofing Methods
Method | Materials | Sustainability | Durability | Cost | Applications |
---|---|---|---|---|---|
Paraffin Wax | Petroleum-based | Low (non-renewable) | Moderate | Low ($0.50/kg) | Frozen food packaging |
Soy/Beeswax | Plant/insect-based | High (compostable) | Low | Medium ($2/kg) | Compostable wraps |
PE Lamination | Polyethylene | Low (non-recyclable) | High | Low ($1/kg) | Milk/juice cartons |
PLA Coating | Cornstarch | High (industrially compostable) | Moderate | Medium ($3/kg) | Cold beverage cups |
Water-Based Acrylics | PFAS-free polymers | Medium (recyclable) | Moderate | Medium ($4/kg) | Fast-food wrappers |
Nanocellulose | Plant nanocrystals | High (recyclable) | High | High ($10/kg) | Luxury packaging |
Seaweed Alginate | Brown seaweed | High (marine-safe) | Low | Medium ($5/kg) | Fresh produce wraps |
Silicone Coatings | Silicone oils | Medium (reusable) | High | High ($8/kg) | Reusable baking sheets |
Aluminum Foil | Aluminum | Medium (recyclable*) | High | Medium ($3/kg) | Pharmaceutical packaging, military rations |
Note: Aluminum foil is recyclable if clean, but laminated paper-foil combos require specialized separation.
3. Waterproof vs. Water-Resistant: What’s the Difference?
Comparison Table
Factor | Waterproof | Water-Resistant |
---|---|---|
Protection Level | Full barrier against liquids and vapor | Partial barrier; delays water ingress |
Durability | Long-term, even under pressure | Short-term or light exposure |
Sustainability | Often less eco-friendly (e.g., PE, foil) | More eco-friendly (e.g., wax, PLA) |
Cost | Higher (e.g., nanocellulose, silicone) | Lower (e.g., wax, water-based coatings) |
Best For | Liquids, medical packaging, outdoor use | Dry foods, short-term storage, branding |
Understanding the distinction between waterproof paper packaging and water-resistant paper packaging is critical when designing or selecting coatings for paper packaging. Here’s how these terms apply to the methods we discussed:
3.1 Waterproof
Definition:
A waterproof paper packaging with barrier completely prevents water penetration under specific conditions (e.g., submersion, prolonged exposure).
Key Features:
-
Impermeable: Blocks liquid water and vapor.
-
Durability: Maintains integrity under pressure or extended exposure.
-
Applications: Ideal for liquids, humid environments, or long-term storage.
Examples from the Blog:
-
Aluminum Foil Lamination: Fully impervious to water when intact.
-
Polyethylene (PE): Creates a plastic-like barrier for milk cartons.
-
Silicone Coatings: Resists water even at high temperatures (e.g., baking parchment).
Limitations:
-
Recycling challenges (e.g., PE-coated paper requires specialized facilities).
-
Sustainability trade-offs (e.g., aluminum’s energy-intensive production).
3.2 Water-Resistant
Definition:
A water-resistant barrier delays or reduces water penetration but does not fully block it. It offers protection against light splashes or short-term exposure.
Key Features:
-
Temporary Protection: Degrades under prolonged or heavy exposure.
-
Flexibility: Often lighter and more eco-friendly than waterproof options.
-
Applications: Dry or semi-moist products (e.g., snacks, baked goods).
Examples from the Blog:
-
Soy/Beeswax Coatings: Resist moisture for compostable food wraps but soften over time.
-
Water-Based Acrylics: Protect against grease and light moisture in pizza boxes.
-
PLA (Polylactic Acid): Moderately resists water but melts under heat.
Limitations:
-
Not suitable for liquids or long-term humid conditions.
-
May require additional layers for robust protection.
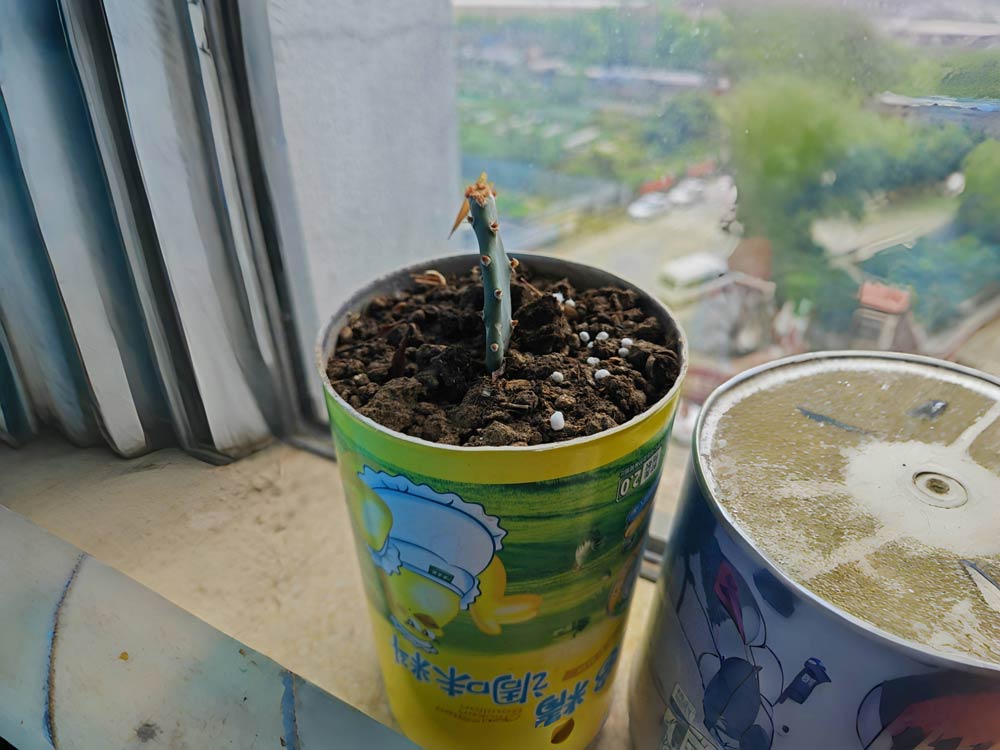
4. Waterproof Paper Packaging: Success Stories
4.1 Tetra Pak’s Bio-Based Cartons
Solution: Replaced 20% of PE with sugarcane-based barriers.
Impact: Reduced carbon footprint by 15% while maintaining recyclability.
4.2 KFC’s PFAS-Free Buckets
Method: Water-based acrylic coatings for grease resistance.
Result: 100% recyclable packaging in the EU.
4.3 Amcor’s Foil-Laminated Pharma Packaging
Innovation: Aluminum foil-paper laminates for moisture-sensitive pill blister packs.
Outcome: Extended drug shelf life while ensuring recyclability through partner programs.
5. How to Choose the Best Waterproofing Method
5.1 Decision-Making Framework
5.1.1 Assess Application Needs
- Liquids: Silicone or PE for robustness.
- Greasy Foods: Water-based acrylics (PFAS-free).
- Dry Goods: Cost-effective paraffin wax.
5.1.2 Evaluate Sustainability Goals
- Compostable: PLA or soy wax (ASTM D6400-certified).
Recyclable: Water-based coatings or aluminum foil (if separable).
Marine-Safe: Seaweed alginate (degrades in seawater).
5.1.3 Budget Considerations
Low-Cost: Paraffin wax ($0.50/kg).
Mid-Range: Water-based acrylics ($4/kg).
Premium: Nanocellulose ($10/kg) for luxury brands.
5.2 Checklist for Selection
☑️ Regulatory Compliance: Ensure FDA/EFSA approval for food contact.
☑️ Infrastructure Alignment: Verify local recycling/composting capabilities.
☑️ Lifecycle Cost: Factor in long-term savings from reduced waste or brand loyalty.
5.3 Expert Insights
Trends: Regulatory pressure (e.g., Maine’s 2030 PFAS ban) favors water-based solutions.
Testing: Conduct moisture resistance tests (ASTM D779) and biodegradability assessments.
5.4 Common Pitfalls
Overlooking Infrastructure: PLA’s compostability is moot without industrial facilities.
Misjudging Exposure: Aluminum foil corrodes in acidic environments; use nanocellulose for acidic products.
Choosing the right method for waterproof paper packaging balances performance, cost, and sustainability. Innovations like nanocellulose and seaweed alginate are reshaping the industry, while traditional methods remain relevant for specific use cases. Always align choices with both operational needs and environmental ethics to stay ahead in the eco-conscious market.
6. The Road Ahead: Emerging Innovations
-
Mycelium Coatings: Waterproof paper packaging’s barriers grown from mushroom roots (e.g., Ecovative for Dell laptops).
-
Enzymatic Treatments: Modifying paper fibers to repel water intrinsically.
-
Self-Healing Barriers: Microcapsules that repair cracks (prototype by DS Smith).
7. FAQs
Q1: Is waterproof paper packaging recyclable?
A: Yes, if coatings are recyclable (e.g., water-based acrylics). PE, PLA, and aluminum foil require specialized systems.
Q2: What’s the most cost-effective method?
A: Paraffin wax ($0.50/kg), but soy wax offers better sustainability.
Q3: Are PFAS-free coatings as effective?
A: Yes! Silicone and clay-based alternatives match PFAS performance.
Q4: Can I compost PLA-coated paper at home?
A: No—PLA requires industrial composting (140°F+).
Q5: Is aluminum foil-laminated paper eco-friendly?
A: Aluminum is recyclable, but separation from paper is energy-intensive. Opt for mono-materials like nanocellulose when possible.
Conclusion
Waterproof paper packaging is revolutionizing sustainable design, offering solutions from aluminum foil laminates to compostable PLA. While traditional methods like foil provide robust barriers, innovations like nanocellulose and mycelium promise greener futures. Brands must weigh durability, cost, and end-of-life impacts to choose wisely.
Audit your packaging today. Swap plastics for innovative waterproof paper packaging solutions and lead the green transition. Contact us to get quote.