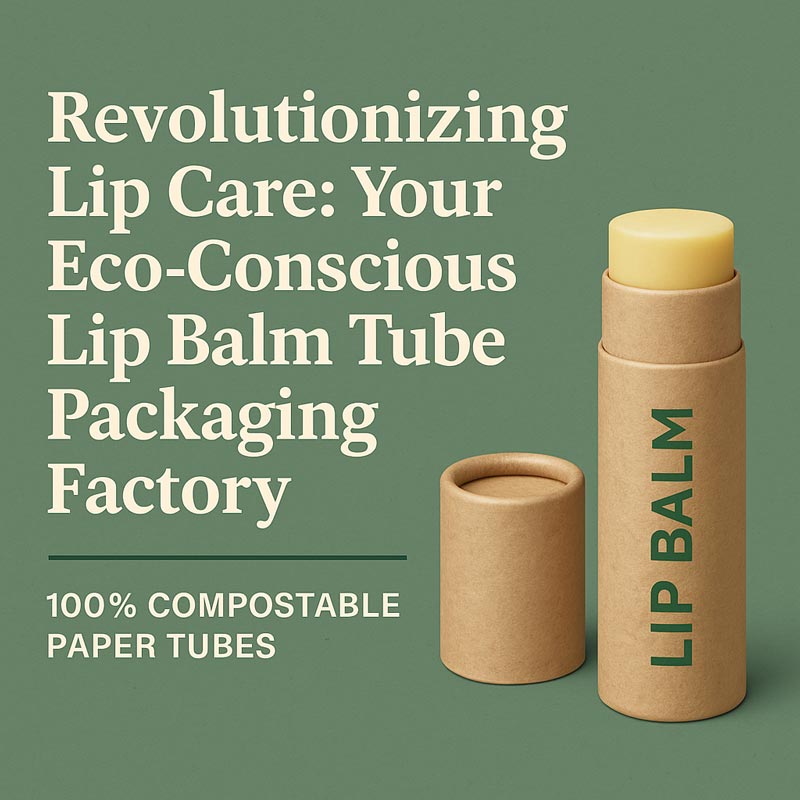
Explore the Best Lip Balm Tube Packaging Factory in 2025
As a trusted lip balm tube packaging factory, we are at the forefront of the sustainable packaging revolution, crafting 100% compostable paper tubes for progressive beauty
Paper tube packaging is a popular and eco-friendly solution for packaging a wide range of products, from cosmetics and food to candles and shipping tubes, thanks to its eco-friendliness and versatility. But how are these tubes actually made? In this article, we’ll take a closer look at the process of how paper tubes are made.
The first step in the process is material selection. Most paper tubes are made using kraft paper, which is a strong, durable paper that is also environmentally friendly. The thickness and weight of the paper will vary depending on the intended use of the tube.
Once the material has been selected, it is cut into long strips and rolled into a spiral shape. The strips are then glued together, creating a solid tube. The diameter of the tube is determined by the width of the strips, and can range from small to very large depending on the application.
To create a rigid structure, a glue is applied to the paper as it’s being wound around the mandrel. Once the paper has been completely wrapped around the mandrel, it’s allowed to dry and set, forming the paper tube’s body.
Once the tube has been created, it is cut to the desired length. This step can be done manually or with the use of a machine, depending on the quantity being produced. And next the ends of the tube are closed. There are a variety of closure options available, including plastic, metal, or paper end caps. The end closures are glued or crimped onto the ends of the tube, creating a secure seal.
Once the tube is complete, it can be printed and labeled. This is often done using a printing press, which can add text, graphics, and other visual elements to the tube. Labels can also be added to the tube, either during the printing process or as a separate step.
Depending on the product, paper tubes can be fitted with various add-ons such as caps, lids, sifters, cut windows, and other types of closures.
Before the tubes are shipped out, they undergo a thorough quality control process. This involves checking the diameter, length, and weight of the tubes, as well as ensuring that they are free from any defects or imperfections.
As a trusted lip balm tube packaging factory, we are at the forefront of the sustainable packaging revolution, crafting 100% compostable paper tubes for progressive beauty
When it comes to manufacturing premium packaging that stands out and adds value to the brand that houses it, there is a crucial component that is
Pinterest In the world of premium fragrance, packaging plays a crucial role in shaping first impressions. Before the scent is even experienced, the customer touches,
If you run a business, especially an online one, you’ve most likely asked yourself at some point: How do I make my packaging more memorable? You’re
When it comes to premium fragrance, the bottle is only part of the story. What truly defines a luxury perfume brand is its packaging —
In today’s wellness and beauty market, essential oils are more than just aromatic products — they are personal rituals, emotional enhancers, and symbols of a
When it comes to beauty packaging, we’re entering a new era — one where the outside of the product matters just as much as what’s
When it comes to delivering a perfect cup of tea, packaging is more than just a pretty box—it’s a vital component of the tea’s quality
It is an easy step, fill out the form and we will be in touch shortly.